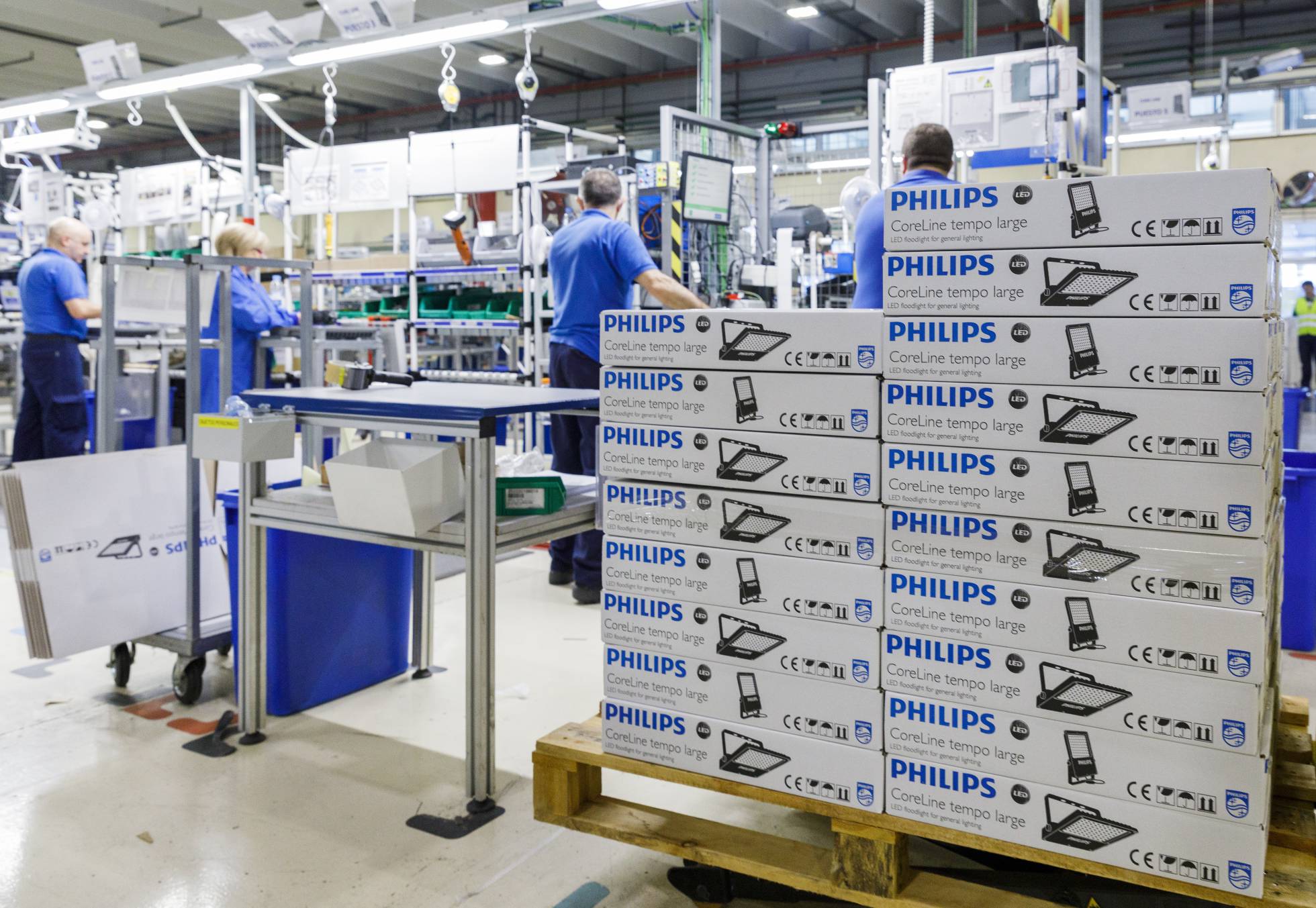
Final del Campeonato de Europa de Fútbol. Pita el árbitro el término de la prórroga con empate en el marcador. Tanda de penaltis. Casi todo el estadio se queda a oscuras: los focos solo apuntan al área donde se juega el partido a todo o nada. Las luces están especialmente diseñadas para que las cámaras ultrarrápidas puedan registrar y transmitir con precisión cada fotograma del evento. El último tiro acierta y el equipo local gana. Con el gol, el estadio estalla en una combinación de luces multicolores, celebrando la victoria. Todo esto, que con la tecnología de hace una década sería fantasía, solo no es posible hoy por las reglas de las federaciones deportivas. Lo demás ya existe, y Philips Lighting, la spin-off de la multinacional holandesa especializado en iluminación, lo diseña, prueba y fabrica en Valladolid.
La revolución de la iluminación gracias a los diodos emisores de luz (led) es el único salvavidas posible para la empresa, que se desgajó en 2016 cuando su matriz decidió centrarse en su división médica y de innovación. La tradicional bombilla incandescente, el invento que en 1891 permitió a Gerald Philips edificar un imperio a partir de una pequeña fábrica en Eindhoven, ha muerto —“salvo para usos muy especializados”, puntualiza el consejero delegado de la firma, Eric Rondolat— y las nuevas tecnologías, aún en desarrollo, no son tan rentables como un invento centenario que necesitaba de reemplazos constantes. En consecuencia, en lo que llevamos de año la facturación volvió a caer un 2,1%, para cerrar el periodo en 5.073 millones de euros.
La facturación cayó un 1,3% en la primera mitad del año, hasta los 3.389 millones de euros
“Hay que entender que la empresa está perdiendo la que siempre ha sido su actividad más rentable”, intenta tranquilizar Rondolat. “Estamos en camino de entregar lo que dijimos a los accionistas cuando llegamos: que íbamos a aumentar la rentabilidad y que hasta el final del año volveríamos a crecer”.
España es un mercado potente para el grupo, que cerró los nueve primeros meses del año con 244 millones de euros de beneficios, casi el doble que en el mismo período del año pasado. “Es un terreno fértil de gente que no le tiene miedo a la tecnología”, considera Eric Rondolat. “Nuestro sistema Hue, de uso doméstico, es una oferta que tiene muchísimo éxito en España, porque la gente entiende que no solo está ahorrando en consumo eléctrico, sino que también les permite decorar su casa a su manera, sin instalación y solo con usar un móvil, que la inmensa mayoría de los españoles tiene”.
Y explica el funcionamiento: “Si estoy solo en el comedor y quiero cenar o trabajar, programo una luz blanca; si tengo una fiesta, no solo puedo hacer que sea multicolor, sino que además puedo hacer que cambie de color conforme el ritmo de la música”. Y los cambios futuros son igualmente prometedores. “Yo en mi casa no tengo interruptores en los pasillos”, explica el consejero delegado. “El sistema reconoce mi presencia y enciende la luz de forma automática”.
La compañía propone bombillas inteligentes activadas por el móvil para uso doméstico
Pero no solo son las casas y las oficinas las que viven esa revolución. Para espacios más grandes, el centro de ese cambio se encuentra en una sala desmagnetizada en el centro de una planta en el polígono de Argales de la capital castellanoleonesa. Aquí, dos líneas de montaje del tamaño de metro y medio de alto por alrededor de 10 de largo encajan térmicamente pequeños diodos —semiconductores del tamaño de la punta de un bolígrafo— en placas del grosor de una espátula que, posteriormente, se introducen en las luminarias, desde las pequeñas para jardines hasta las gigantescas, que se usan en estadios de fútbol, como el recién inaugurado Wanda Metropolitano de Madrid.
El cambio de modelo de negocio llevó a Philips a reducir sus factorías en Europa de nueve a cuatro, pero para Arturo González, director de la fábrica de Valladolid, las 535 personas que trabajan en la factoría están tranquilas: “Está claro que aquí no tenemos los costes laborales que tienen en Hungría y Polonia, pero tenemos la infraestructura, el conocimiento y el modelo logístico. Somos la fábrica más pequeña de todas, pero la más eficiente, y aquí es donde hacemos los productos de mayor valor añadido”. Aparte, claro, de la calidad de vida. “Levanto la mano y tengo diez holandeses queriendo venir a vivir aquí”.
La fábrica de Valladolid es la más pequeña, pero fabrica los productos de mayor valor añadido
Otra de las fortalezas de la factoría es el laboratorio, en el que se somete a los productos del grupo a pruebas de luminosidad, resistencia a las fluctuaciones de corriente y temperatura. “Durante 15 días les hacemos todas las perrerías que le pueden pasar en 15 años”, explica González, que recuerda que las exigencias del mercado son mucho mayores. “Es como los coches; antes, en cualquier taller te hacían un apaño, mientras que ahora, sin la maquinita, no tienes ni por dónde empezar”, considera. “Antes, cada 4 años se revisaban las luminarias; ahora ya son casi 20”.
Uno de los puntos fuertes de la batería de pruebas es el chorro de agua a presión al que se someten las luminarias para certificar su estanqueidad, una necesidad derivada de la nueva tecnología. “Antes las farolas emitían tanto calor que no había problemas con el agua”, explica González. “Ahora, como son componentes electrónicos, cada gota de agua las estropea”.
Para el consejero delegado de Philips Lighting, el futuro apunta brillante. “Creo muchísimo en el punto de luz conectado”, considera. “Con eso podemos dar al cliente un estudio completo de cómo está utilizando un espacio de trabajo, y proponerle alternativas para mejorarlo y optimizarlo”. Y, sobre todo, dar un servicio sobre el ciclo de vida completo; la luz como servicio y no solo como equipamiento. “En un almacén hemos instalado el equivalente a 30 kilómetros de fuentes de luz, y ellos no pagaron por la instalación”, explica Rondolat. “Pidieron un préstamo y lo van pagando con lo que ahorran en energía. Es un modelo de negocio de lo más atractivo”.